International Coatings IC-505 Optilux Reflective Plastisol Ink Coupler
International Coatings IC-505 Optilux Reflective Plastisol Ink Coupler
Couldn't load pickup availability
Payment & Security

Your payment information is processed securely. We do not store credit card details nor have access to your credit card information.
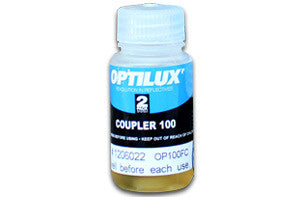
- DESCRIPTION
- REVIEWS
Increase Night-Time Visibility With International Coatings IC-505 Optilux Reflective Plastisol Ink Coupler
Optilux™ Ultra Reflective Ink Systems
Optilux™ 505 Ultra Reflective Plastisol is an easy to print, two-part, retro-reflective ink that contains light-reflecting microspheres. When a garment printed with Optilux™ 505 ink is exposed to a focused beam of light, such as that from a flashlight or an automobile headlight, it reflects or returns light back to the light source.
Optilux™ 505 Ultra Reflective Plastisol can be used as a unique decorative tool to increase night-time visibility of a printed design.
Optilux™ Application
To obtain the best reflective properties, Optilux™ 505 is recommended for use on open weaved fabrics. Optilux™ can also be used with very good to excellent results on some tightly woven nylon and polyester fabrics. Optilux™ 505 is not a low bleed product and is not recommended for use on bleeding fabrics.
Nylon and Polyester Fabrics
Print Optilux™ 505 ink through a 160 t/in to 230 t/in (63 t/cm to 90 t/cm) Monofilament screen. Use one flood stroke and one print stroke for best results. Two print strokes can be used for added opacity when printing through a 230-mesh t/in (90 t/cm).
On tightly woven fabrics such as shell nylon, a flash cured underbase print of the 900 or 9000 Series nylon inks may be used to gain opacity, colour and a smoother looking print. Printing Optilux™ 505 over an underbase may diminish the reflective strength of the ink to a small degree but for some nylon or polyester fabrics, it is best to print over an underbase in order to obtain the cleanest print of the Optilux™ 505 ink. Printing Optilux™ 505 ink onto some tightly woven nylon or polyester materials without an underbase may leave the print looking pockmarked as the ink may not flow properly on some of these fabrics.
Always test for adhesion when printing onto any tightly woven material such as shell nylon. Water-resistant or waterproof coatings on some nylon or polyester fabric may prevent proper adhesion of Optilux™ 505.
On some polyester materials, bleeding or dye migration may occur. These types of fabric should be tested prior to beginning any production of finished product. Bleeding or dye migration might not occur immediately, so longer term testing of the ink film is strongly recommended when printing polyester or polyester blend fabrics.
Cotton and Cotton / Poly Blends Fabrics
Print Optilux™ 505 ink through a 160 t/in to 230 t/in (63 t/cm to 90 t/cm) Monofilament screen. Use one flood stroke and one print stroke for best results. Two print strokes can be used for added opacity when printing through 230-mesh t/in (90 t/cm). Adding pigment to Optilux™ 505 ink will shade the ink slightly to a desired colour, but adding too much pigment will diminish the reflective properties of the ink.
Note: It is not recommended to print Optilux™ 505 ink over an underbase print when printing on open weaved fabrics such as typical T-shirt type fabric.
Technical Information
Ink Preparation: Optilux™ 505 ink must be mixed thoroughly with Optilux™ 100 Coupler before printing in order to obtain best wash and wear durability. Optilux™ 100 Coupler is provided in 2 fluid oz. (60 ml) and 8 fluid oz. (250 ml) containers. Stir thoroughly into the Optilux™ 505 ultra reflective ink prior to use. The recommended proportions are:
By weight: 20 grams of ink to 1 gram of Optilux™ 100 Coupler.
Pot life of mixed ink is approximately 8 to 12 hours. Do not mix more ink than is needed for the job. Any mixed ink not used within 12 hours should not be used again.
Screen Application: Use 160 t/in to 230 t/in (63 t/cm to 90 t/cm) Monofilament. Printing through a coarser mesh may reduce the reflective quality of the ink.
Use a 110 t/in to 160 t/in (43 t/cm to 63 t/cm) for an underbase prints on tightly woven fabrics.
Use any direct lacquer resistant emulsion or capillary film.
Squeegee: 60-70 Durometer: Sharp Edge
Ink Cure Temperature: 325°F (163°C) entire ink film. Test dryer temperatures and wash test printed product before and during a production run.
Clean-Up: Mineral Spirits or any environmentally friendly plastisol screen wash.
Packaging: Quart, 1 Gallon, or 5 Gallon Containers.
Storage of Ink Containers: Recommend storage at 65°F to 90°F (18°C to 32°C). Avoid storage in direct sunlight. Keep containers well sealed.
Product Material Safety Data Sheets:
Optilux™ IC-505 Relective Plastisol Ink
Optilux™ IC-100 Optilux Coupler
Viewing Instructions: Hang printed garment in a dark room so that the printed portion of the design is fully visible. Stand directly back from the print, 10 feet or more, and hold a flashlight next to your head, eye level and point the light directly at the print. Light should be reflected directly back to the viewer.
Important Information: Optilux™ 505 Ultra Reflective Inks are ready for use as supplied. For best results, product should not be modified with any viscosity reducers or thickeners. Viscosity of this product is already low and any modifications can result in poor reflective quality.
Always stir Optilux™ 505 Ultra Reflective Inks thoroughly prior to each use. The reflective microspheres used in the ink will settle in the container when ink is stored for any length of time. The retro-reflective properties of Optilux™ 505 Ultra Reflective Ink can be diminished by using an improper screen mesh, under-curing, by adding other inks, pigments or additives to the ink.
Always pre-test this product before using in production. Check for reflectivity, opacity, adhesion, wash durability and any other attributes that are required for your particular application.
For best long term wash durability of printed fabric, machine wash finished product in cold water, delicate cycle, and wash inside out. Do not use bleach. Do not iron on printed area of garment. Recommend line or hang dry. The reflective quality of the Optilux™ 505 product should improve after the first washing.
Additional Information
505 Optilux Reflective Instruction Manual