The dip tank is an efficient and effective tool for all screen printers. Read about the benefits.
How to Effectively Reclaim With a Dip Tank
They are also easy to use and integrate into your pre- and post-press screen printing process. The dip tank helps users realize efficiencies that are otherwise difficult to attain. Dip tanks are useful not only for reclaiming purposes, but also in supporting the stencil-development process. Pre-press production is one of the best (and often overlooked) ways to use a dip tank because it makes stencil development after exposure much easier and much more consistent, especially for the beginner screen printer. Below are the top 5 benefits of dip tanks.
1. Dip tanks are Versatile - Maximizing Their Many Purposes
Most people who are against using dip tanks typically think of them as a one-step clean-up solution and nothing more. They believe that is the product's main purpose. However, other applications, such as aiding in stencil reclamation and developing are truly helpful uses of the dip tank as well. The latter two functions work under almost all shop conditions.
It's the one-step, or all-in-one screen cleaning capacity that has drawbacks, but these are easy to void. Usually, these drawbacks are related to purchasing the proper dip tank solution. Not all products are created equal. Some are just better than others. For example the Lawson One-Step Dip Tank Solution. It also has to do with a screen printer’s internal process. Factors such as how thick the emulsion stencils are, how much plastisol or water-based ink is scraped out, and how old the screen is matters. Some people buy a dip tank, gather up all their old screens that have been sitting around the past year and try to reclaim them. It is not surprising the dip tank did not magically work - neither will reclaiming them by hand.
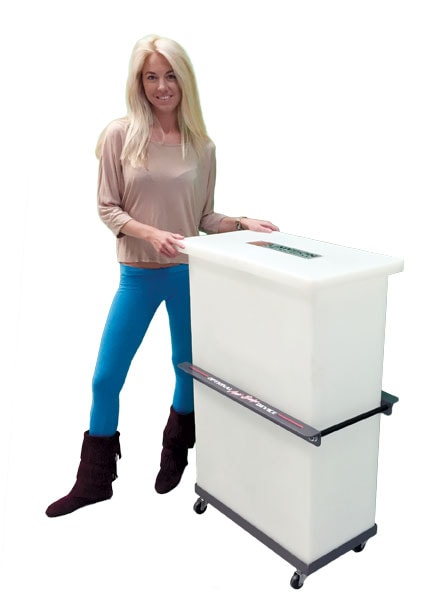
Some stencil materials are easier to reclaim than others. Understanding your emulsion is important. For example, a water-resistant emulsion reclaims differently than a solvent-resistant stencil because the former is a water-resistant emulsion to begin with! Experimentation is key, but expect a decline in effectiveness if you attempt to treat stencil build-up with heavy capillary films or thick-film (high-density) emulsions.
Printers also need to scrape out their screen inks before using the dip tank for a one-step frame cleaning process. Those who don't do a good job of carding out their ink from the screen tend to struggle more with a dip tank (just like they would reclaiming by hand). It's not going to work because the one-step chemistry can only use a mild ink degradent. Using a really strong ink degradent in a dip tank competes with the stencil-remover solution.
2. Dip Tanks Are Simple To Use
Dip tanks are probably the simplest pieces of hardware in any screen-printing shop. Most are polypropylene tanks on stands with a spigot for easily emptying them. If you have a properly designed unit, it won't leak. Nothing will stick to the sides. They're maintenance-free pieces of screen printing equipment and are relatively inexpensive. Purchasing a dip tank that can accommodate several screens at once saves time. After soaking your screen print frames in a One-Step solution for about 5 minutes, all you have to do is power wash your printing frame. Nothing could be easier.
3. The Economical Benefits of Using Dip Tanks
The traditional way to reclaim a stencil is to scrub a stencil-removing solution and let it set (be careful not to let it dry as that will “lock in” the image and ruin your screen). The reality is that your stencil removing solution runs down the frame and mesh and is quickly washed down the drain. A dip tank uses the same chemicals again and again. Periodically changing out the dip tank chemical is significantly less expensive than spraying a chemical solution on a screen only to send it straight down the drain a minute later.
When you use a one-step or all-in-one product dip tank solution, you can expect between 200-400 screens with a one-step cleaning solution. A lot of times you can extend this even longer by reactivating the stencil-removing solution. You can do this by adding in some concentrated solution, such as Lawson SR-45 Stencil Remover, or you add in more Kleen Screen Cleaning Crystals to beef it up. This helps prevent switching the dip tank One-Step Solution even less just by giving it a boost.
4. Dip Tanks Don't Damage Your Frames
Most retensionable and aluminum screen printing frames are welded well enough so that water can’t get inside. Roller-frame manufacturers all claim that their rollers are water-tight. However, if a roller frame has a leak, then you'll hear the water sloshing around in it, which can be a problem. Water and chemicals also may get into the frame during other processes, like when you take it to a wash out booth sink and manually reclaim your screen printing frame.
Dip Tank Chemicals are Drain Safe
Local regulations related to waste disposal apply whether you use a dip tank or not. If you're not supposed to send anything down your drain, a dip tank is helpful because you could drain the tank into a drum and have the drum hauled off. This method of disposal ties in with the economical benefits of using a dip tank described earlier.
The reality is the one step dip tank solutions are generally drain-safe in most parts of the country. If you've carded away and scraped out any excess ink, the degradent should successfully break down any remaining residue on your frame or mesh.
Conclusion Using a dip tank to remove screen printing ink and stencil from a screen is a simple tool for making post-production and screen printing clean up easier. It is an easy way to keep reclaiming going without any of the “elbow grease” typically necessary. Getting your pre and post-production process set up for dip tanks is incredibly easy. Sophisticated screen printing shops use dip tanks for BOTH stencil reclamation and developing.